From aerospace to automotive: Friction Stir Welding (FSW) crosses into new sectors
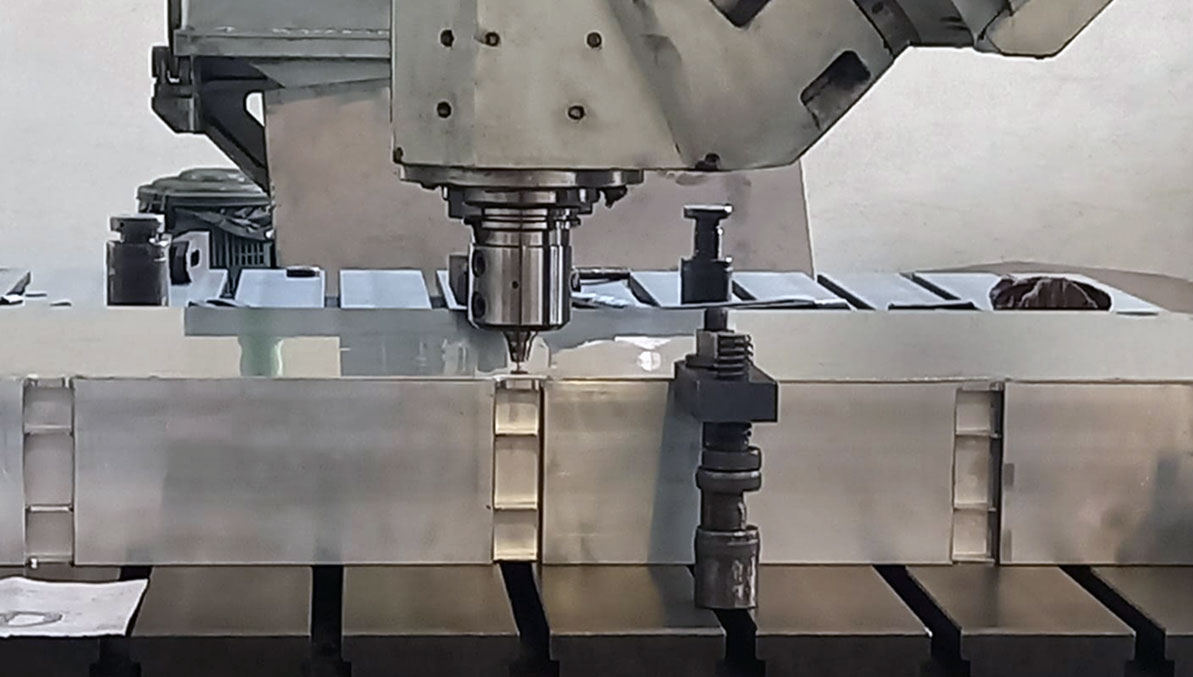
Innovation and experimental successes for Eurodies assembly technologies
Eurodies has been conducting research on friction jointing technology known as Friction Stir Welding (FSW) in collaboration with the Politecnico di Torino since 2020.
Known and used for decades in the aerospace sector, its application in the automotive sector is only now beginning to take its first steps, thanks to the new requirements posed by electric vehicles. Components that are safer, lighter and easier to handle throughout their life cycle are driving the increasing use of aluminum alloys. The machining and joining processes of these materials require major technological innovations to ensure the desired degree of safety and quality in the final product.
Eurodies conducted the first studies in collaboration with the interdepartmental laboratory J-Tech of the Politecnico di Torino by experimenting with innovative tools and processes applied to materials that are of interest to the automotive sector. From these experiences emerged new prototypes of battery cases for electric vehicles.
An exemplary project: the battery case
The design of specific tools for FSW welding was key in the creation of our battery case prototypes and led Eurodies to find new performance solutions in joining sheet metal components and foundry castings. To reduce mass, avoid water infiltration and prevent any leakage of hazardous liquids into the environment, the battery case is made of aluminum alloy and must meet the most stringent sealing regulations, for both liquids and fire.
In particular, the joints of the different elements constitute one of the most critical issues in the execution of the component, determining its quality and durability. Besides ensuring the necessary mechanical strength of the joints, it’s also necessary to ensure that joining dissimilar alloys does not result in technological and microstructural defects, and that thermal deformations created by the process itself are extremely small, so that the dimensional and geometric tolerances of the component are respected.
The sustainability and safety of a car are built into every one of its components
Prototyping is an integral part of the larger process that has led the industry to integrate traditional know-how with new criteria and guidelines. The approval of the UN’s 2030 Agenda incentivizes the development of technologies that save energy and promote sustainability. These goals entail investments that impact the entire production chain: from manufacturing processes to the choice of materials, from the selection of advanced components to the development and fine-tuning of new processing and assembly methods. And as is often the case, the auto industry is leading the way and is among the first sectors to engage in this technological evolution.
The development of the electric car has redefined the production process of every component. The search for welding solutions for the battery case, which has specific shapes and sizes for each model, thus fits into a broader picture: it’s more than just a new industrial approach; it’s an excellent example of how industrial heritage and laboratory research become one with the needs of the increasingly challenging real market.